- MAAG
- / Gears
- / Gears for vertical roller mills /
- MAAG® GEAR MAX Drive System
MAAG® GEAR MAX Drive System
Powerful drive system for peak performance in vertical roller mills. With twin drives delivering maximum power, our MAAG® GEAR MAX Drive System builds on our proven track record and rises to the need for increased capacity in your vertical roller mills. The robust reliability of this three-stage drive system is further enhanced by the torque split, self-aligning pinions and flexible coupling.
True strength from our modular drive system for vertical roller mills
Our three-stage spur gear unit with torque split, the MAAG® GEAR MAX Drive system uses two equal drive units to deliver power up to 15,000 kW for your vertical roller mill. We’ve taken the expertise in gear technologies and manufacturing we’ve built up over the last 100 years and applied them to this modular drive concept specifically for vertical mills. The matched drive units, torque split, reliable components and our proven track record make our MAX Drive an ideal fit for cement and slag grinding – bringing maximum power to your vertical roller mill.

Plainly powerful
The modular concept of the MAAG® GEAR MAX Drive System allow for a compact arrangement without unnecessarily increasing the complexity of monitoring and the connection to the power grid. The two drive units include a vertical asynchronous motor directly flanged to the casing and are each connected to a central girth gear.
When both drives are running, the MAX Drive has a power range from 5,000 to 15,000 kW. You can also operate just one drive, allowing you to continue production at reduced output while performing maintenance on the other drive unit or half of the rollers.
In perfect balance
The power behind our MAX Drive comes from two equal gear units that operate the girth gear around the central part on two flanks. These twin gear units transmit power from the electric motors to the grinding table and reduce the motor’s speed to precisely what you require for the grinding process.
In addition to enabling its compact size, the torque split of our three-stage MAAG® GEAR MAX Drive ensures that the total torque to the mill is always equally distributed between the two pinions. The highly flexible couplings used in the MAX Drive automatically equalise any torque imbalances between the two pinions – ensuring equal load distribution between the two gear trains in each drive unit. The coupling also allows you to adjust the correct timing between the output pinions and the central girth gear and guarantees smooth operations through its damping of torque peaks and adaptable stiffness.
The pinions are also self-aligning, providing full tooth contact, even if there is a small run-out failure at the girth gear set-up. The self-alignment is made possible by a crowned toothing between the pinion and pinion shaft.
Innovative design
Mounted on the output disc, the central part of the MAX Drive System supports the grinding table, while a tilting-pad thrust bearing absorbs the static and dynamic grinding forces. With a design adapted from our well-proven MAAG® GEAR WPU and WPV gear units, the thrust bearing for the MAAG® GEAR MAX Drive System consists of thrust pads lined with Babbitt metal. The bearing is hydrostatically and hydrodynamically lubricated by high- and low-pressure oil pumps and the temperature is continuously monitored.
Dependable components
We use the latest machines and manufacturing processes, ensuring all parts are fit-for-use and free from defects. Our girth gears are made from fabricated steel, which produces a homogeneous crystal structure in the base material of the toothing, contributing to higher fatigue- and wear-resistance. Additionally, our in-house heat treatment eliminates internal stresses in the toothings. You can have confidence in the durability and reliability of the MAX Drive System and its components.
Our comprehensive documentation for the MAAG® GEAR product line allows us to supply spare parts for all gear units since 1926 – giving you confidence that your MAX Drive System will be in good repair for decades to come.
One system, one source
Manufacturing the complete drive system ensures the ideal adjustment between the main motors and all geared parts – and lets us efficiently customise the MAX Drive System to meet your specific requirements. The drive system is available as standard solution or can be customised to suit your unique operational needs.
The design of our MAX Drive System is based on our proven technology – with an eye towards the future and the high-powered needs of the ever-evolving cement industry.
Uncomplicated maximum power
Profit from the compact size
Smooth function and operational reliability
Simplified upkeep
Equal load distribution delivers high efficiency
Three-stage spur gear unit drive system with torque split
The complete MAX Drive System contains:
Two equal drive units, the girth gear unit, the oil unit, the maintenance drive, and a condition monitoring system.
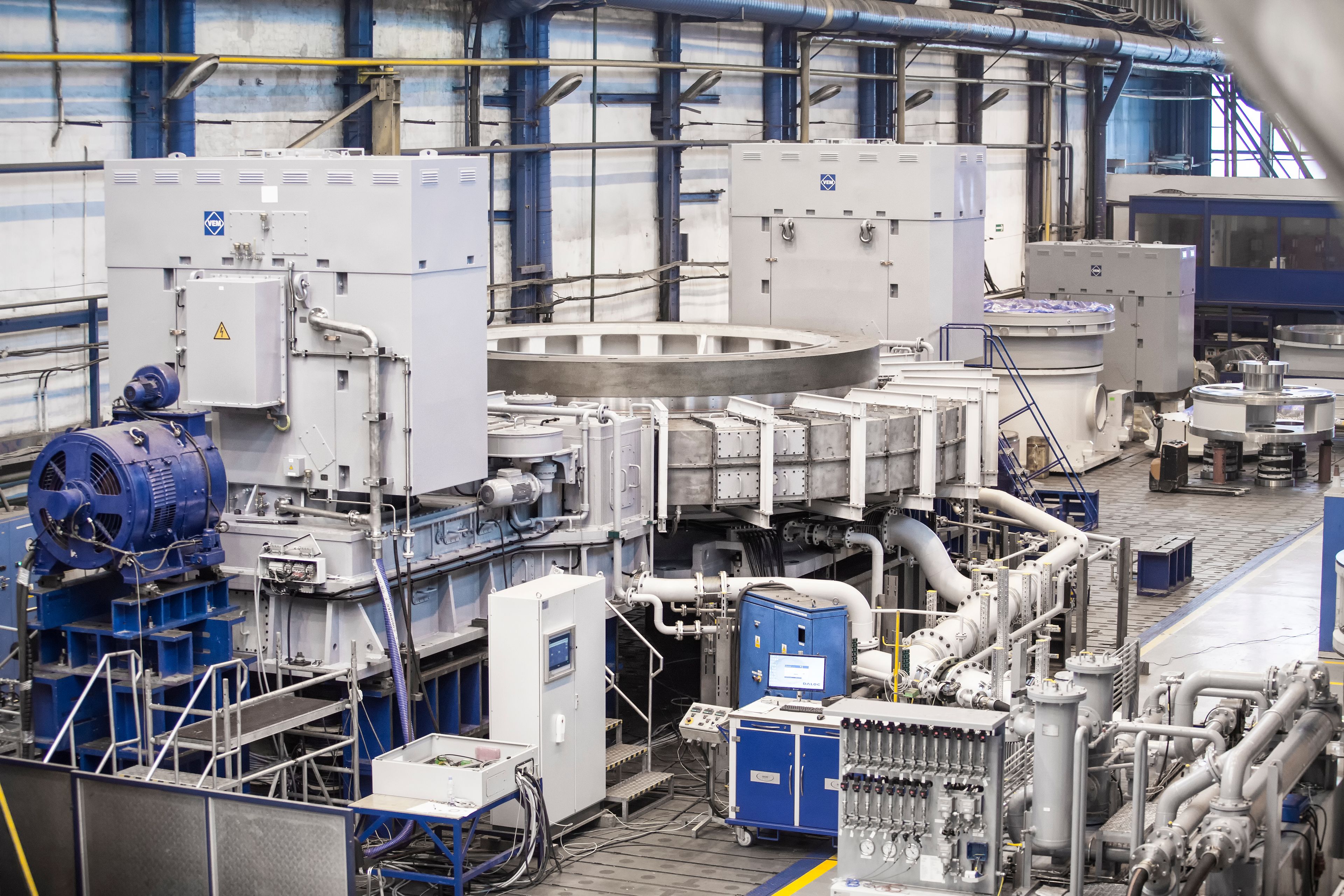
Gearing with stamina
Made up of two or four segments, the girth gear of the MAX Drive is a fabricated design and is manufactured to be more fatigue- and wear-resistant. The ring with the toothing is a high-quality alloy steel that is rolled and bent, while the rib is made out of ordinary carbon steel and welded to the ring.
Specialised power
The compact gearbox of our MAAG® GEAR MAX Drive System is powered by a vertical electric motor, adapted from a standard design to specifically fit this application. It is a squirrel cage asynchronous motor mounted directly on top of the gear casing, removing the need for any complicated onsite alignment.
Shielded by sealing
In order to protect the girth gear from dust, we developed a new sealing concept that decouples the drives from the central part. A labyrinth seal, brush and dust protection shield are installed between the mill table and girth gear guard, along with rubber sealing to protect the central part and gear unit. These safeguards allow the drive system to run smoothly and decrease servicing.
Oil supply unit keeps the gear unit running smoothly
The oil supply units for our vertical roller mill gear units and drive systems includes low-pressure pumps to feed bearings and toothings with filtered and cooled lubrication oil. If required, high-pressure pumps supply the oil for the thrust bearing from a separated compartment of the tank filled with filtered oil from the low-pressure part. Using only clean oil on the high-pressure side allows us to improve the lifespan of the pumps.
Simple handling with the maintenance drive
The maintenance drive is integrated in one of the gear trains and allows you to rotate the mill table very slowly. This simplifies maintenance work at your vertical roller mill, including replacing lining plates or rebuilding surfaces through welding.
Beyond a basic condition monitoring system
All of our gear units and drive systems are equipped with unparalleled condition monitoring sensors. Normally, these types of sensors keep an eye on critical operating parameters like bearing temperatures, casing vibrations, etc. and trigger a mill shutdown in the case of exceedances.
Our condition monitoring system does much more. It lets you set up condition-based preventive maintenance that uses continuous monitoring and data analysis to detect wear and tear at an early stage. With this enhanced information, we help you plan maintenance and servicing in advance – reducing downtime and keeping your plant running smoothly.
Downloads
Condition Monitoring Systems
PDF (3.30 MB)
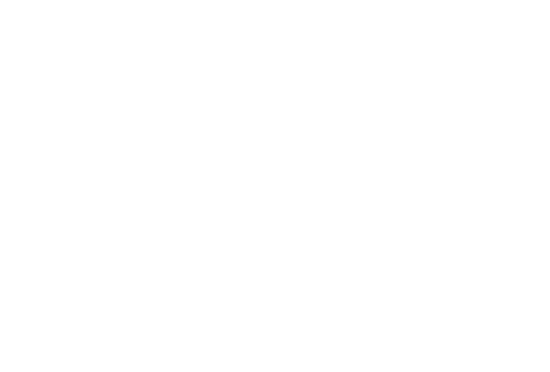
Join our newsletter.
Don’t miss out on the latest news, updates,
and insights - from MAAG.
© copyright MAAG Gear 2025. All rights reserved.
MAAG GEAR
INDUSTRIES
SERVICE CENTER
INDUSTRIES
SERVICE CENTER